GOODYEAR-METHOD - THE CREATION OF A GOODYEAR-WELTED SHOE
A classic, welted Ludwig Reiter shoe is manufactured according to the Goodyear-method in around 300 steps by highly qualified craftsmen at the
Ludwig Reiter Shoemanufactory in Vienna, Süßenbrunn. This method, which is still mastered and used by only a few shoe producers worldwide,
gives the shoes a special degree of durability, wearing comfort and finesse.
The classic technique of welt sewing is still the unsurpassed, internationally most renowned and therefore very timeless way of producing shoes of the highest quality:
a beautiful example of Ludwig Reiter's leitmotif: “The future of tradition”.
From the cutting of the leather to the final stitch, every step is meticulously done by hand, a few of which are described in detail here:
The Ludwig Reiter Team shown with a Goodyear-welted Budapester.
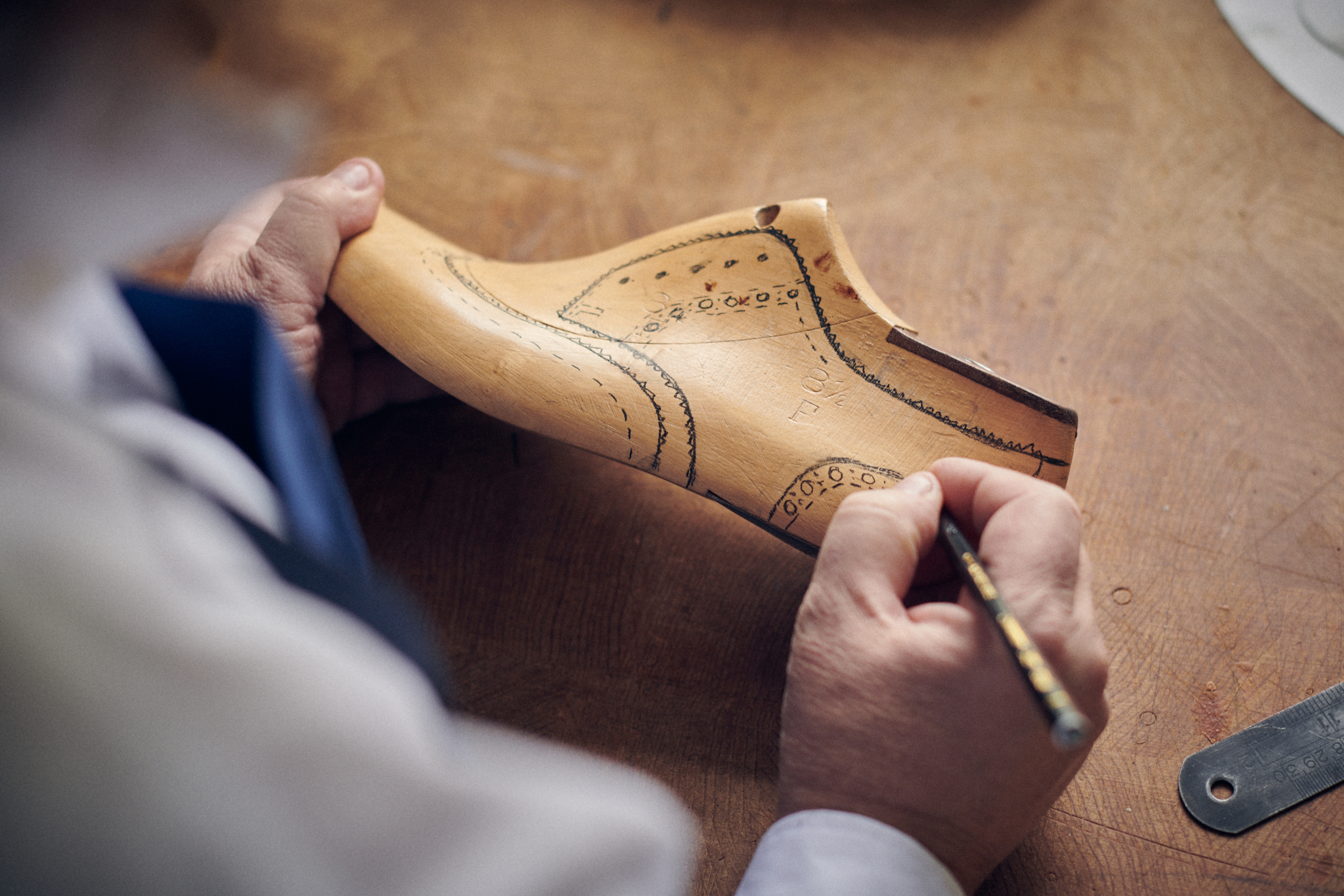
the last - the soul of the shoe
Each new development of a shoe model requires the skills of a last modeller who creates a new model based on a wooden last. The resulting last gives each shoe its own unique characteristics and fit.
Quality control
We source leather and raw materials from tanneries in Italy, France and Germany. Some special leathers like bison and horse leather come from America because of the unique quality.
In this step, the leather is meticulously searched and marked for small natural defects (e.g. wrinkles, mosquito bites etc.) so that these can be taken into account for when cutting. These faults are not a sign of inferior quality, on the contrary they show that the leather can still 'breathe' and has not been wiped of its essential natural characteristics like breathability, durability and longevity.
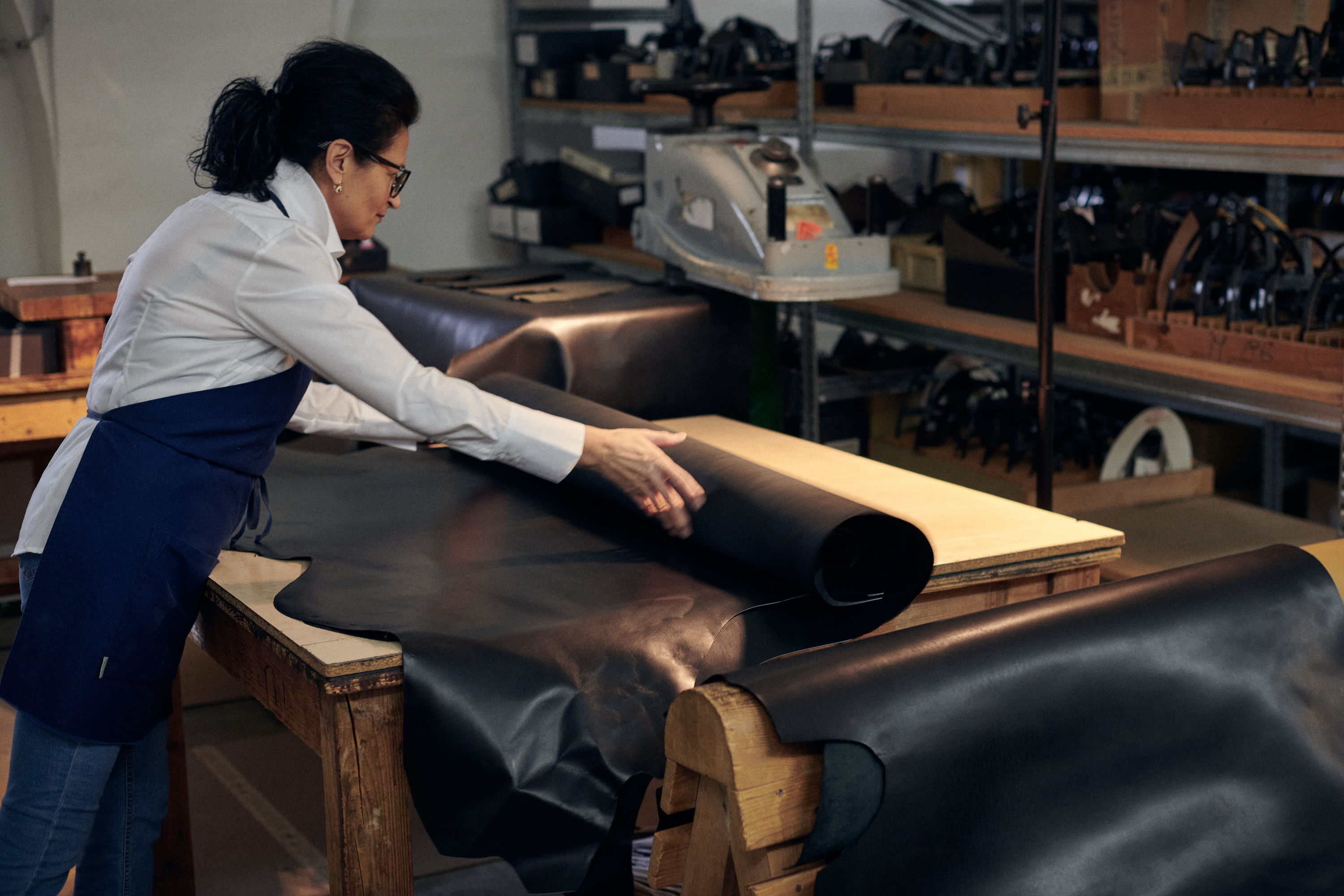
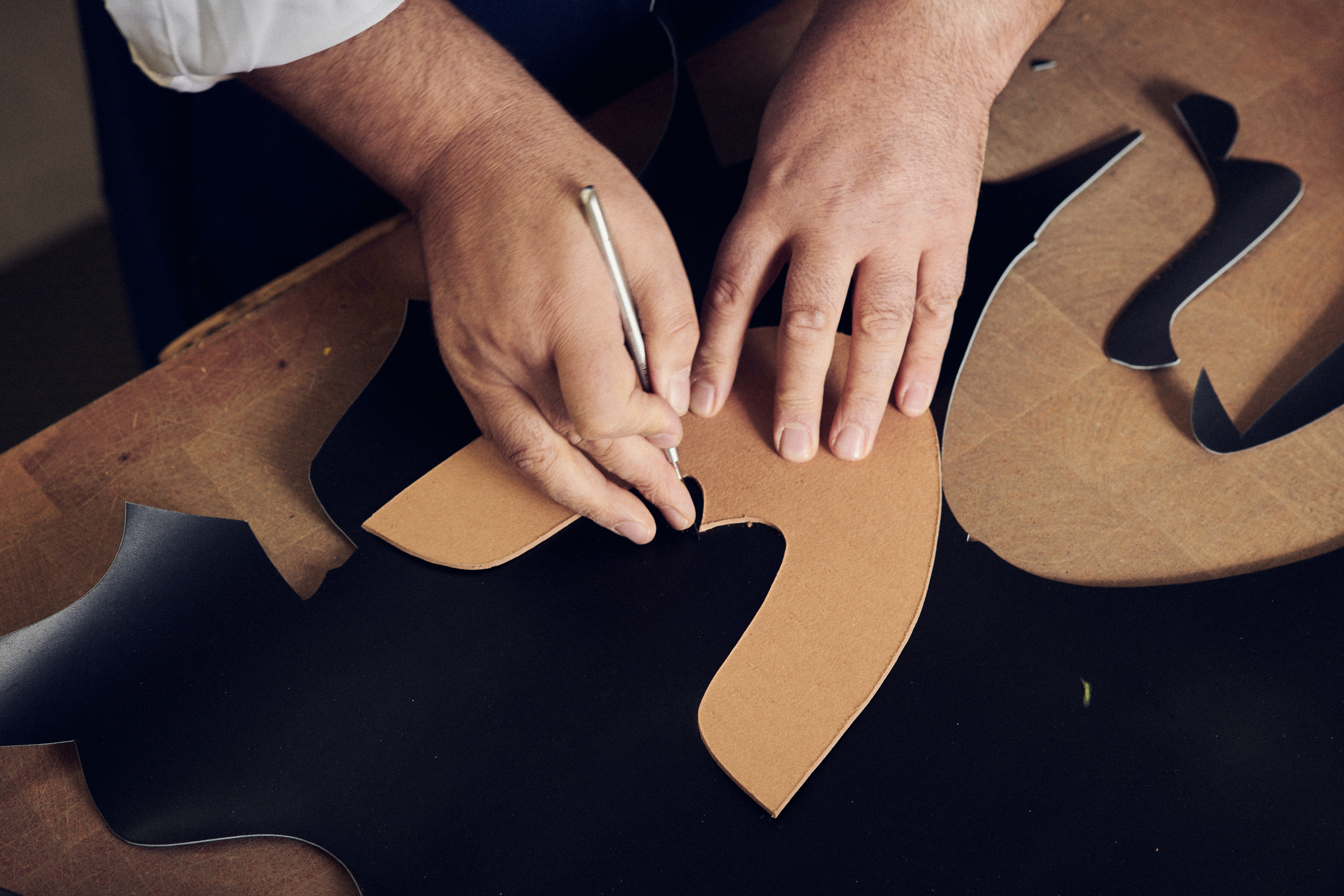
clicking
The individual elements of the shoe are cut, or as cobblers would call it 'clicked', with the aid of a template and knife. This work step requires a particularly high level of knowledge with the material and is carried out by very experienced craftsmen.
PERFORation with precision
The model 'Budapester', which is crafted in this picture, is distinguished by a special pattern, which is perforated carefully using one of the oldest sewing machines of the Ludwig Reiter shoe manufactory. The perforations are made without templates and therefore require a particular fingertip precision.
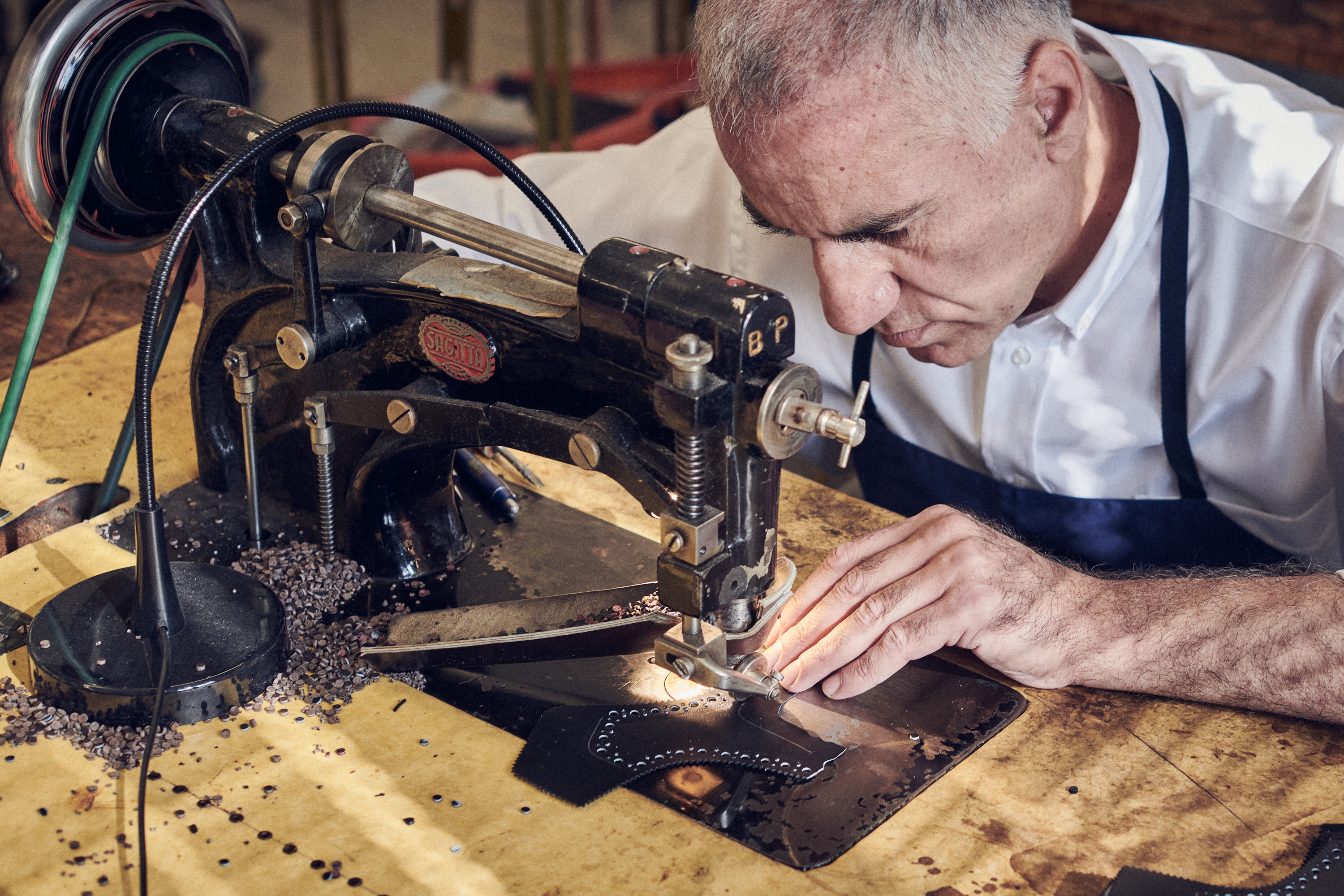
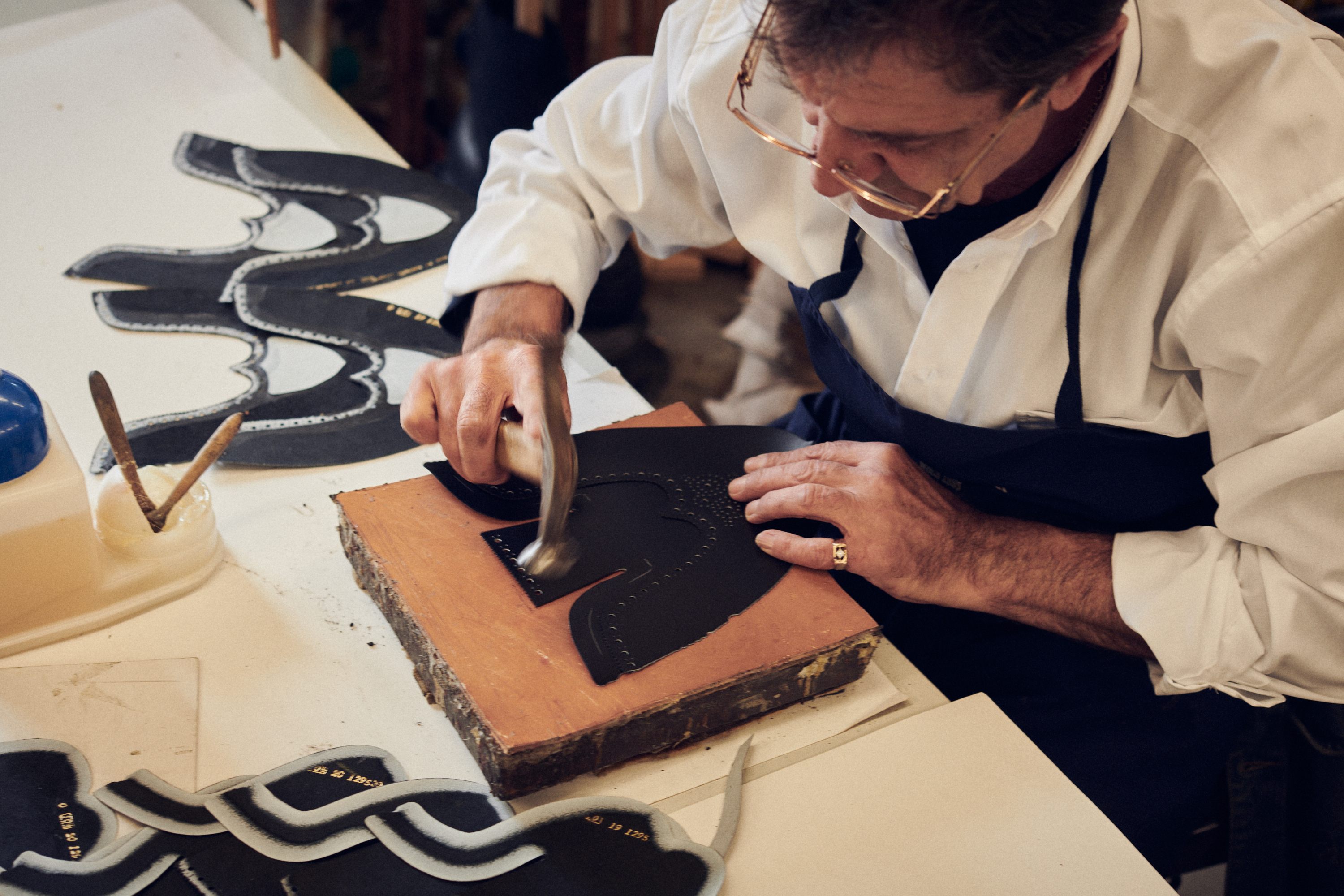
PIECING IT ALL TOGETHER
The individual parts of the leather uppers are assembled by hand and thus prepared for the next step, sewing the uppers together.
TOP STITCH
The elements of the uppers and the lining are sewn together in many individual operations. Each stitch must sit perfectly, if it goes out of place, you usually have to start all over again.
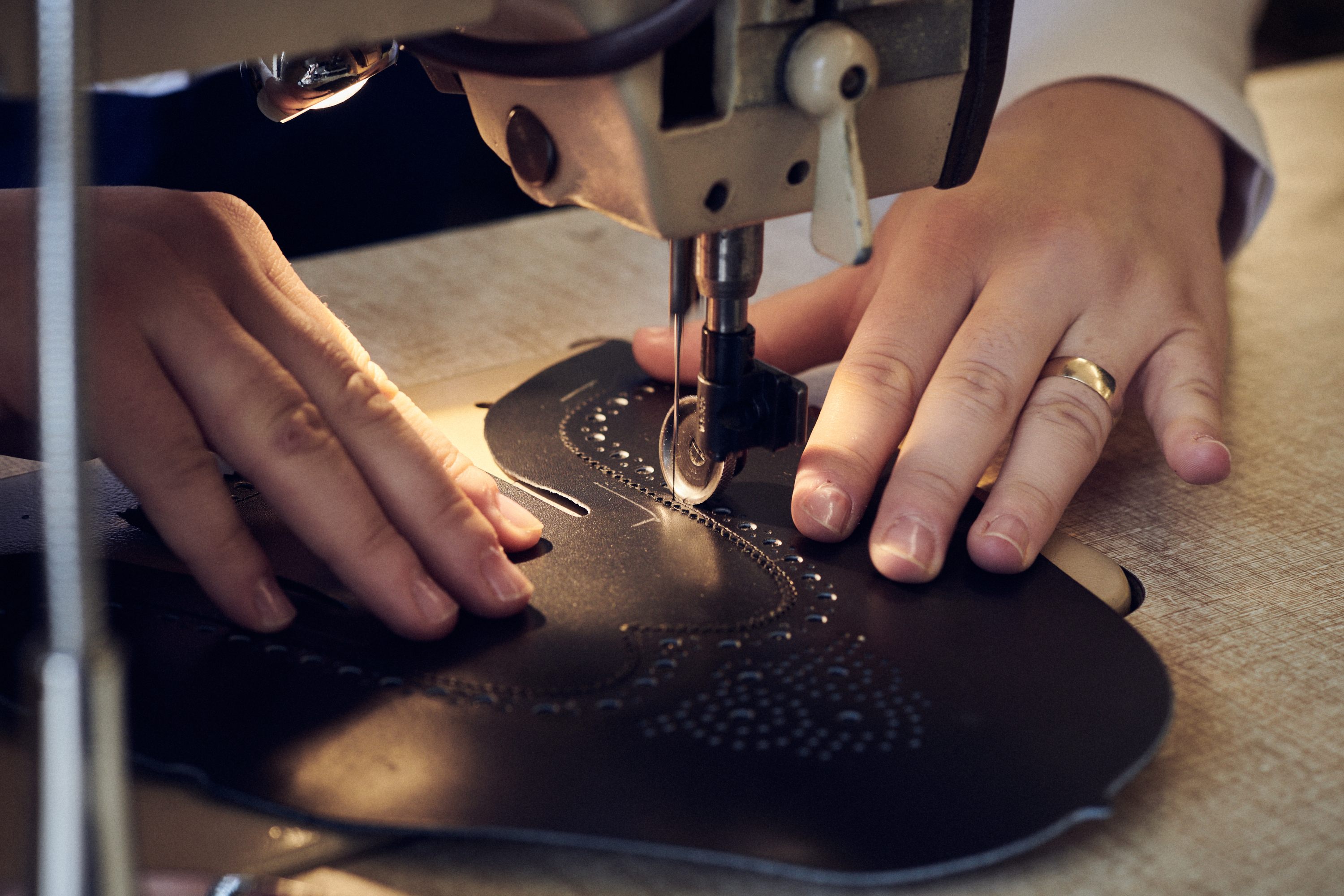
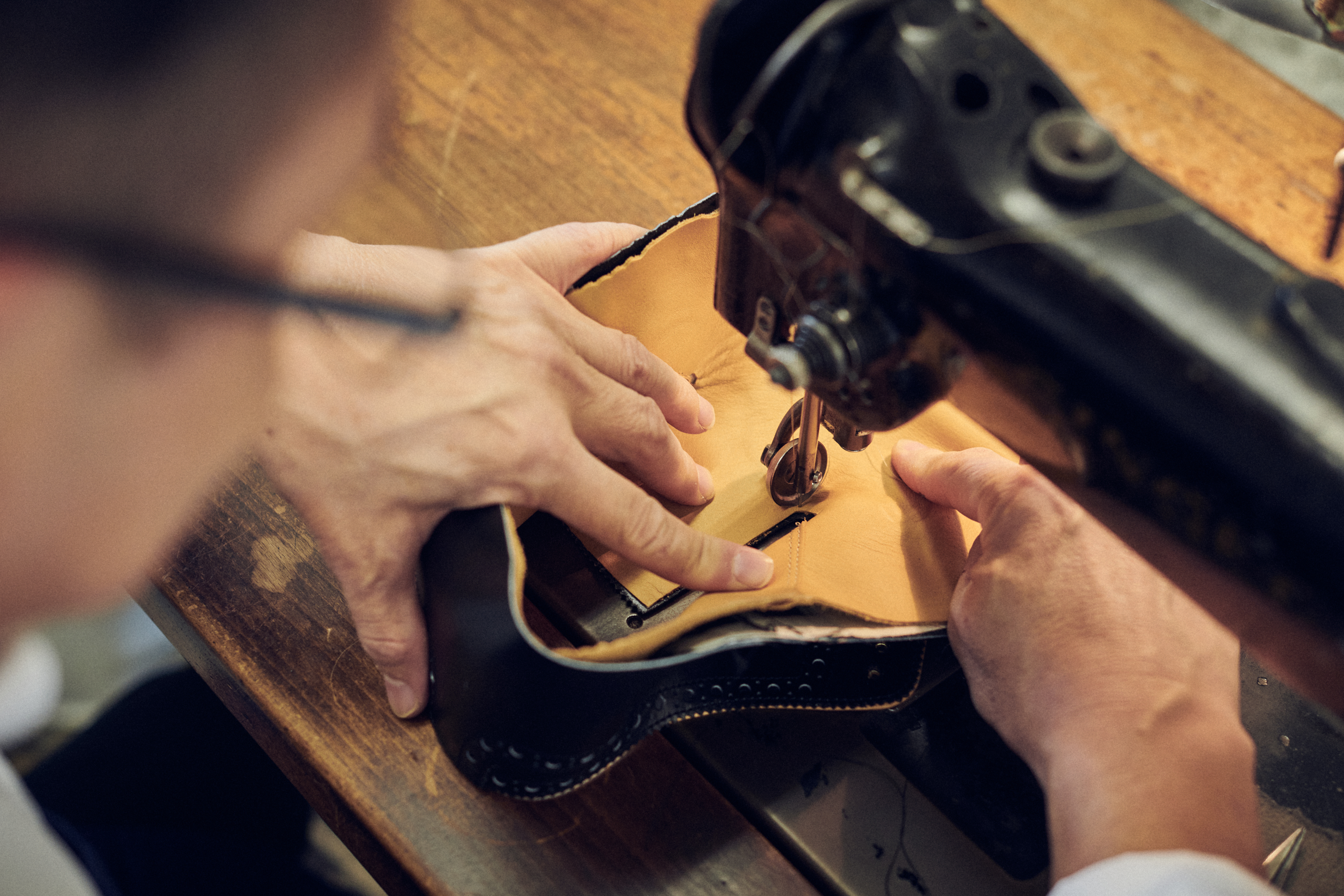
THE LEATHER LINING
In this step, the upper leather is connected to the leather liningand then sewn together. The leather lining plays an important role because it is just as important for the 'shoe climate' as the upper leather, as it has to absorb a large part of the foot's moisture.lasting anD mounting
The leather uppers are now sewn and will be joined to the sole in the following steps. The last, which defines the character and shape of the shoe, is inserted and remains in the shoe until it is finished.
The tip of the upper leather is stretched over the last and then side-stitched to the insole. The insole is the part of the bottom of the shoe on which the foot stands and is therefore made of natural untreated cowhide.
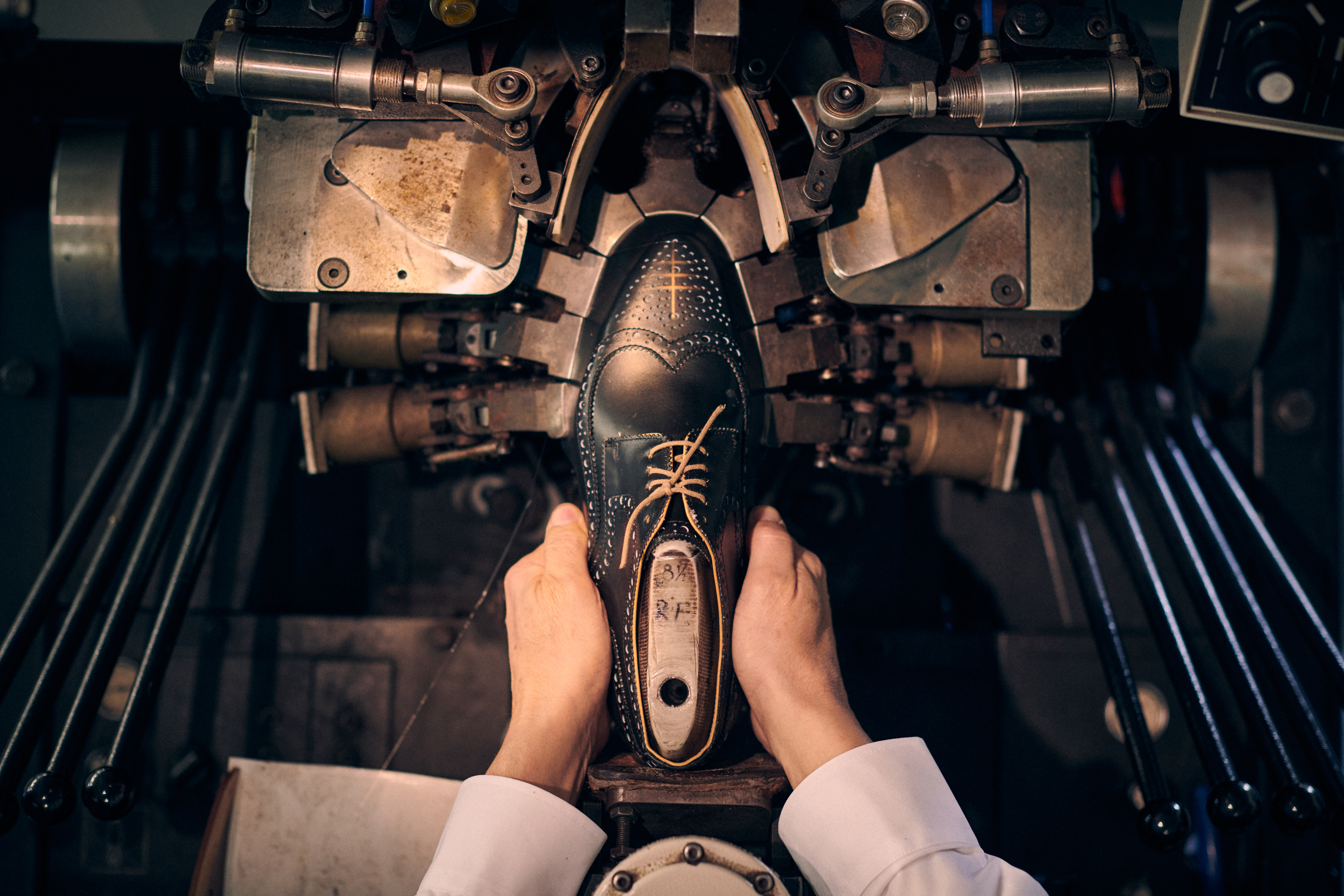
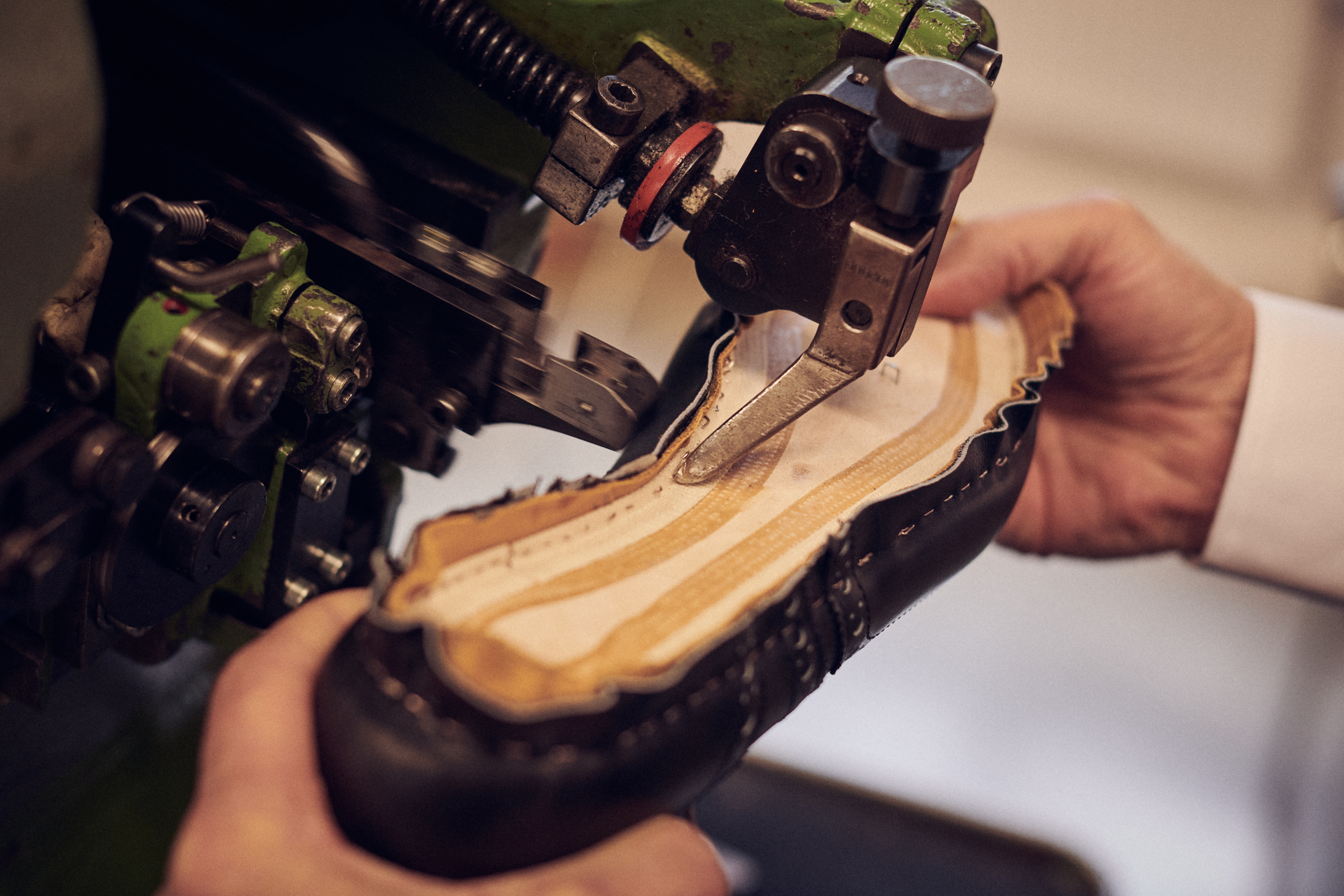
SiDE TWEAKING
The shoe is tweaked on the sides: the upper leather is pulled over the last and pinched together with the insole. The insole is the part of the bottom of the shoe on which the foot stands and is therefore made of first-class untreated cowhide.
TECHNOLOGY TRANSFER
Frame sewing, which was previously carried out exclusively by hand with awls, needles and thread, was mechanized and rationalized primarily by several special sewing machines patented in the United States in 1872 by the American Charles Goodyear Junior. This is where the term “Goodyear-welted” comes from.
Ludwig Reiter II, the son of the company founder, worked for several years in the Endicott Johnson shoe manufactory in the United States of America at the beginning of the 20th century and learned about mechanical Goodyear-welting there.
In 1909 when he returned, he brought the Goodyear method to Vienna, acquired the corresponding machines and gradually converted his father's craft business into a shoe manufactory.
Since then, hardly anything has changed from a technological point of view at Ludwig Reiter. The machines from the early days are still in use today in order to craft unique pairs of Goodyear-welted shoes.
Ludwig Reiter II (front left) on his way to the USA on a steamship in 1902.
The Goodyear frame piercing machine, which has been in use at the Ludwig Reiter Shoemanufactory since 1920.
Colleagues of Ludwig Reiter II at the Shoemanufactory Endicott Johnson in Massachusetts (Ludwig Reiter II third from left).
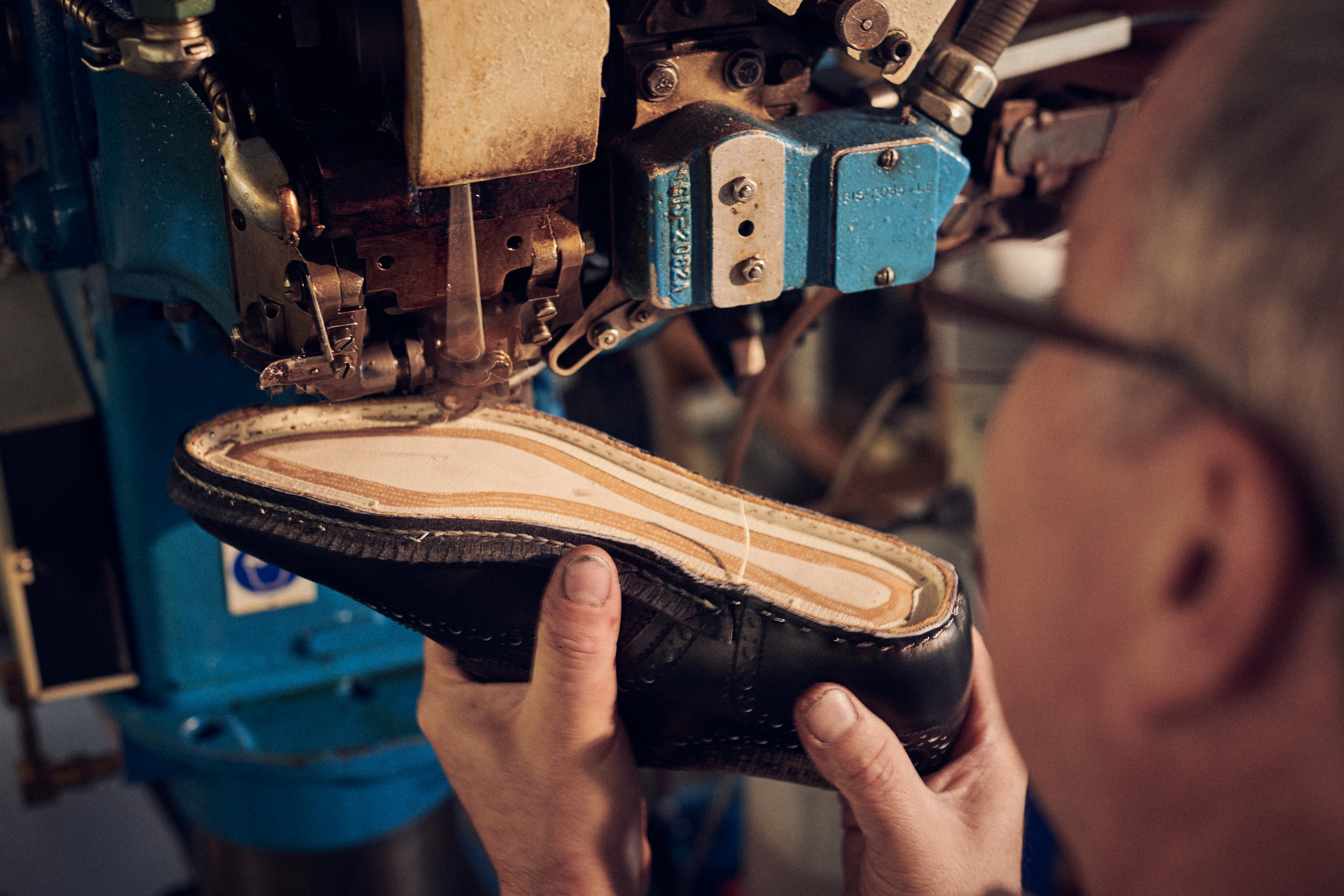
goodyear-welting
The particular challenge in making a shoe is to join the upper to the bottom of the shoe in such a way that the shoe is soft, comfortable, elastic and yet strong and durable. In itself a contradiction, but one that is resolved by welted sewing, in which the upper is joined to the outsole by two separate seams that are both flexible and durable. To do this, first the upper and the insole are sewn together with a leather welt running around the shoe.
optimal wearing comfort
In order to further increase the wearing comfort of the welted shoe, the space between the insole and the outsole is filled with cork compound, into which a wooden plate made of maple wood - the wooden joint - is inserted for stabilization and shock absorption.
Another advantage of Goodyear-welted shoes with leather soles is that there is no barrier layer made of plastic or adhesive between the sole of the foot and the bottom of the shoe, which would hinder skin breathing. The air permeability of the leather is important because there are a lot of sweat pores on the sole of the foot.
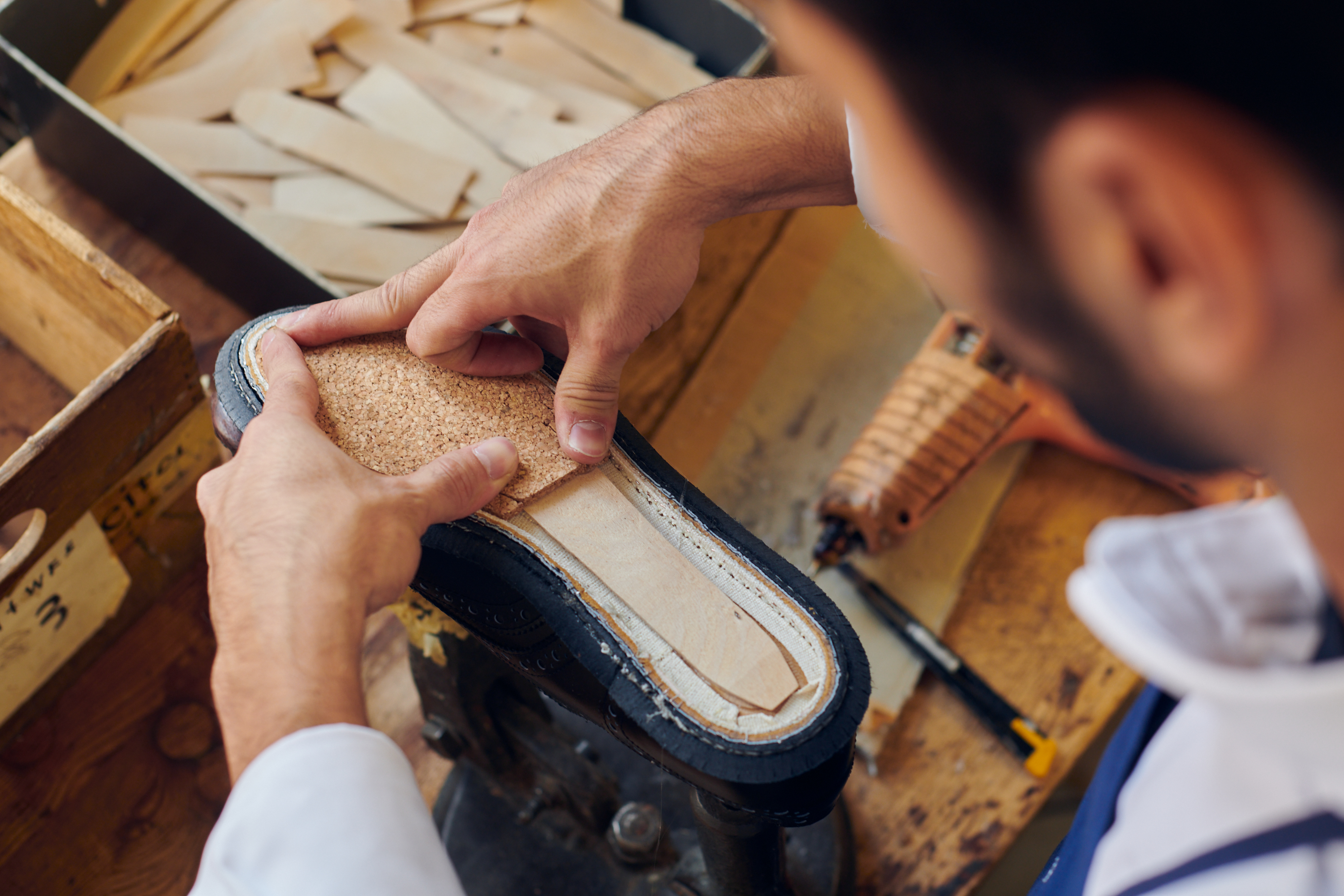
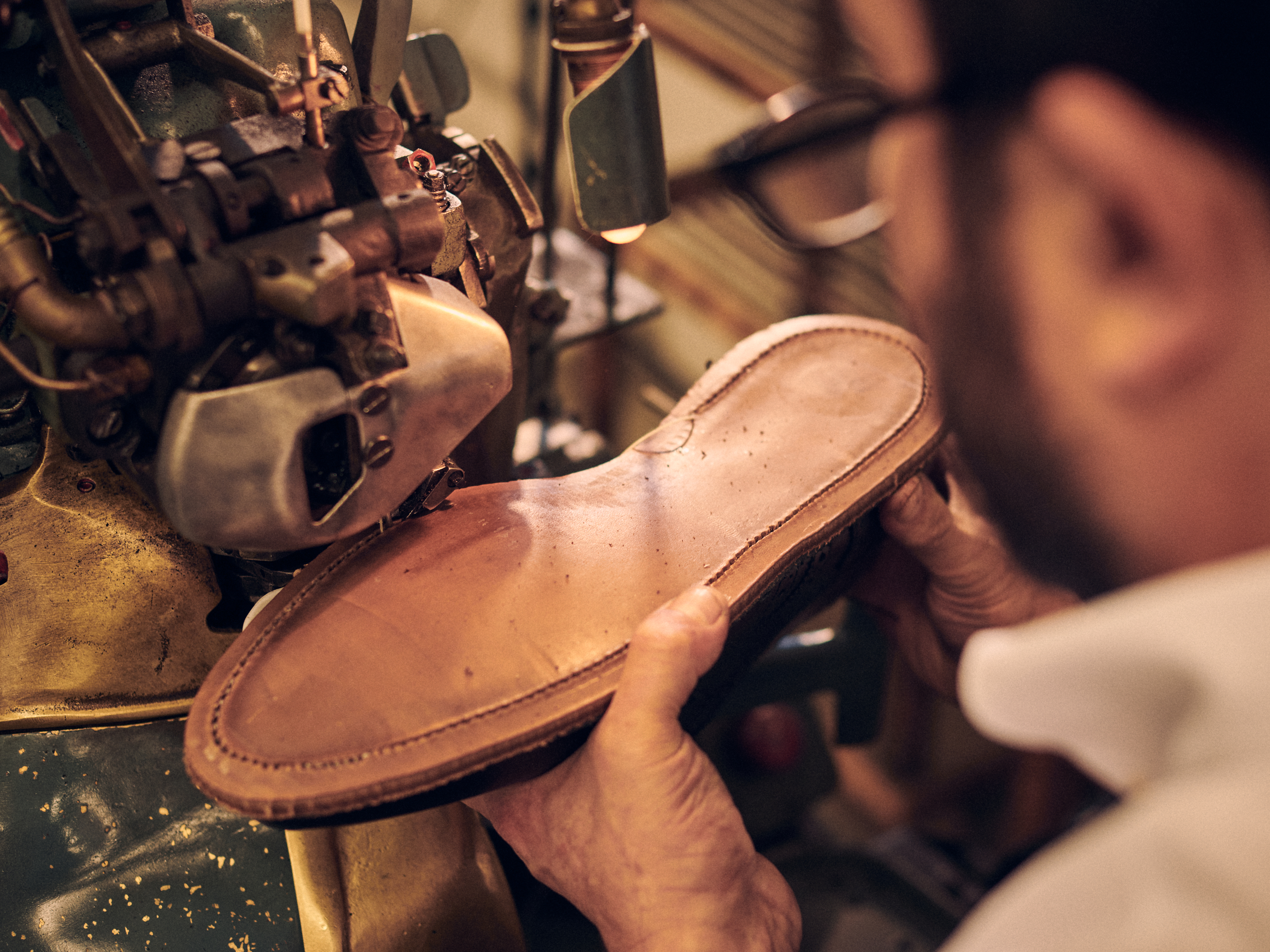
the flexible center
In a further, separate step, doubling, the frame is connected to the leather sole with a second seam. The upper part of the shoe and the sole are not connected directly, but indirectly and flexibly.
The entire shoe is built around a “movable” center – the frame – which allows the shoe to flexibly follow the extremely complex movement sequence of the foot when walking. This ensures maximum comfort.
the leather heel
After milling the edge of the sole, the leather heel is pressed on from several layers of cowhide, milled, glazed, the bottom of the shoe is blown, and the heel and cut are polished.
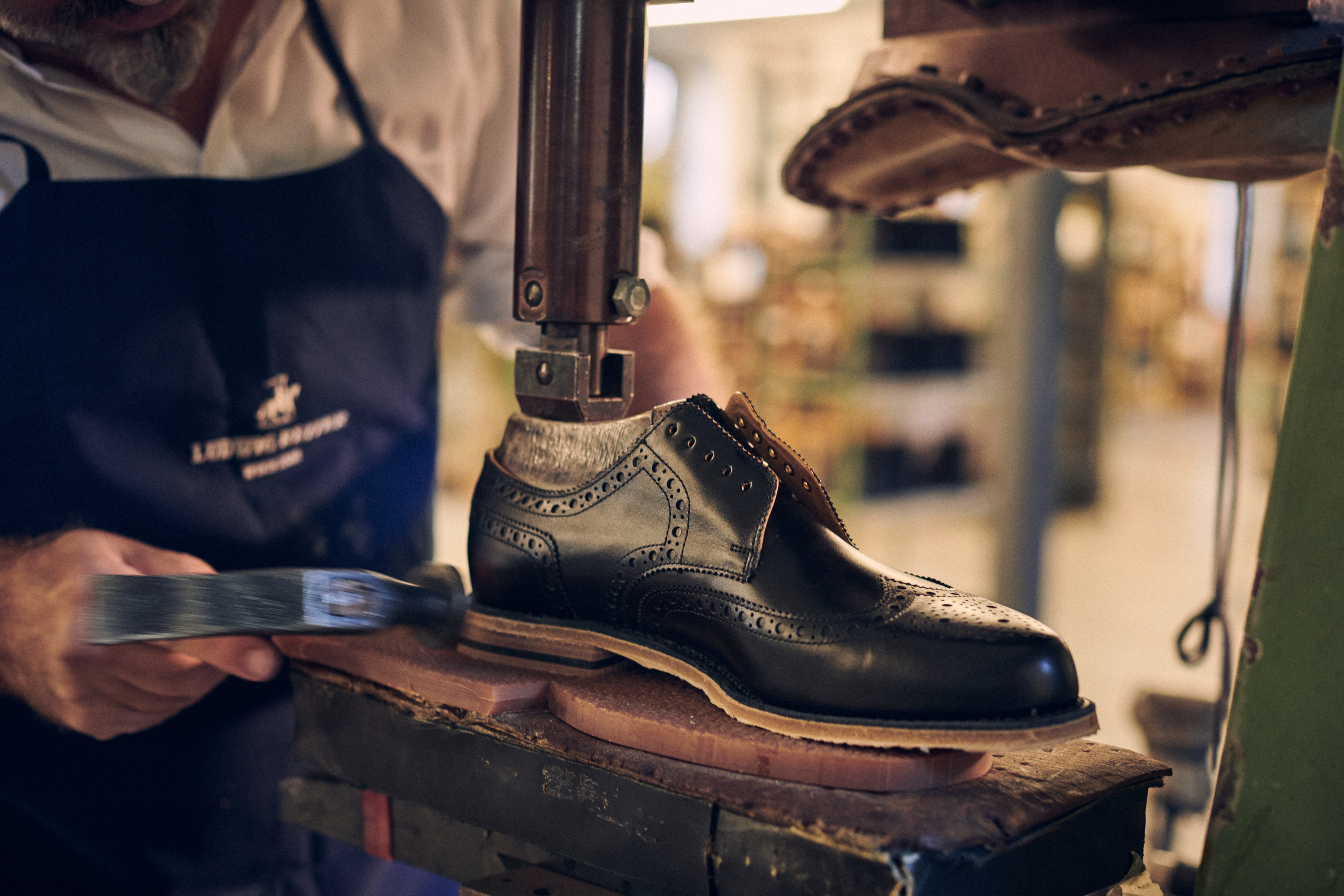
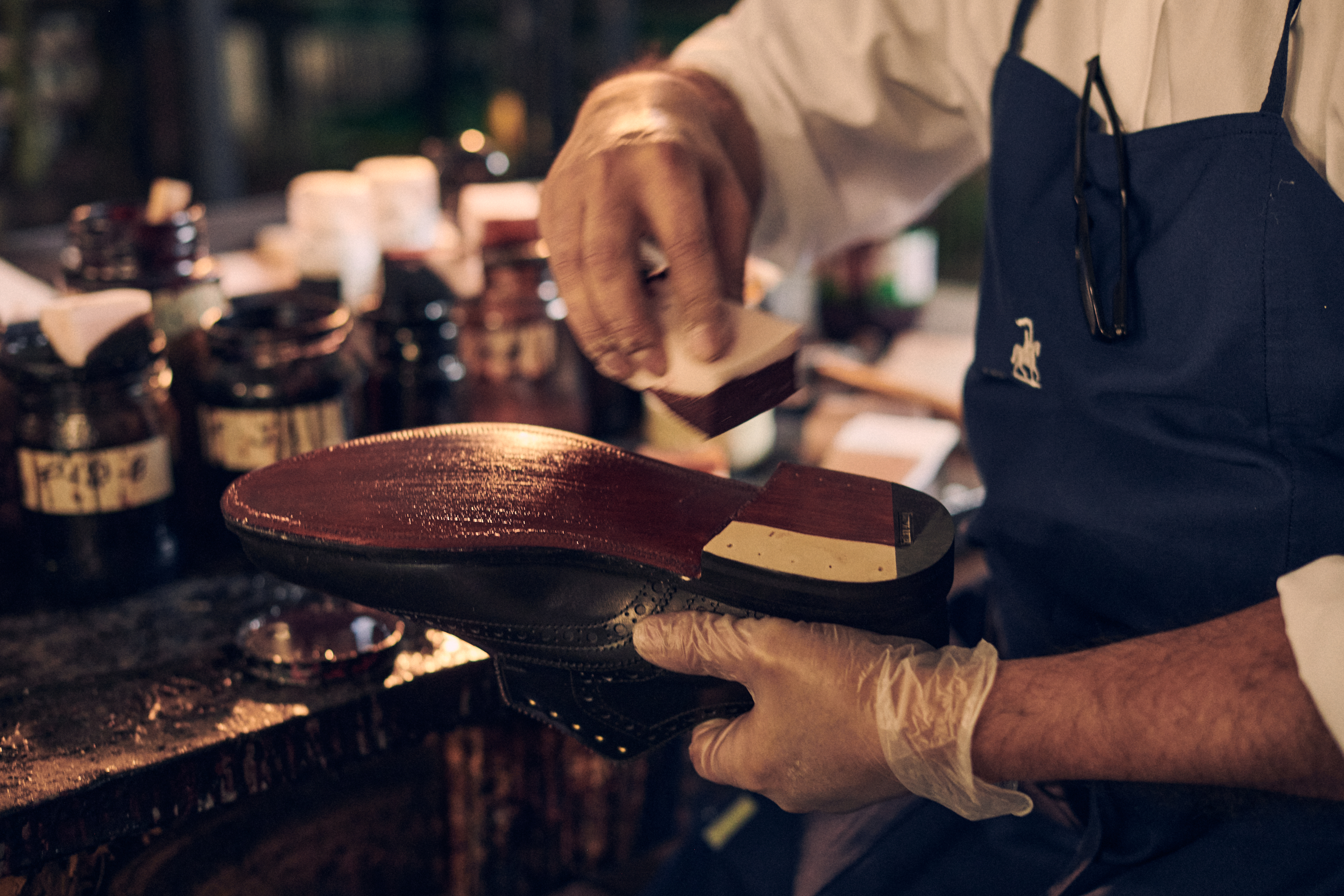
a special characteristic - the leather sole
A classic Goodyear-welted Ludwig Reiter shoe with a leather sole has an unmistakable feature. It is processed with several shades of shoe paste and then provided with an embossing stamp.
C'EST FINI(SH)!
In the so-called finish, the upper leather is treated with shoe paste, polished and the heel patch is installed. The shoe is subjected to a precise quality and final inspection by the trained eyes of our employees.
Et voilà!
Goodyear welted shoes need to be worn in for a while before they offer optimal comfort. The leather first has to get used to the shape of the foot, the leather insole and the cork layer underneath need some time to form an individually adapted footbed.
So it's not just their durability, but above all the special wearing comfort resulting from the construction of the two elastic seams and the cork insert that makes Goodyear-welted shoes so unique.
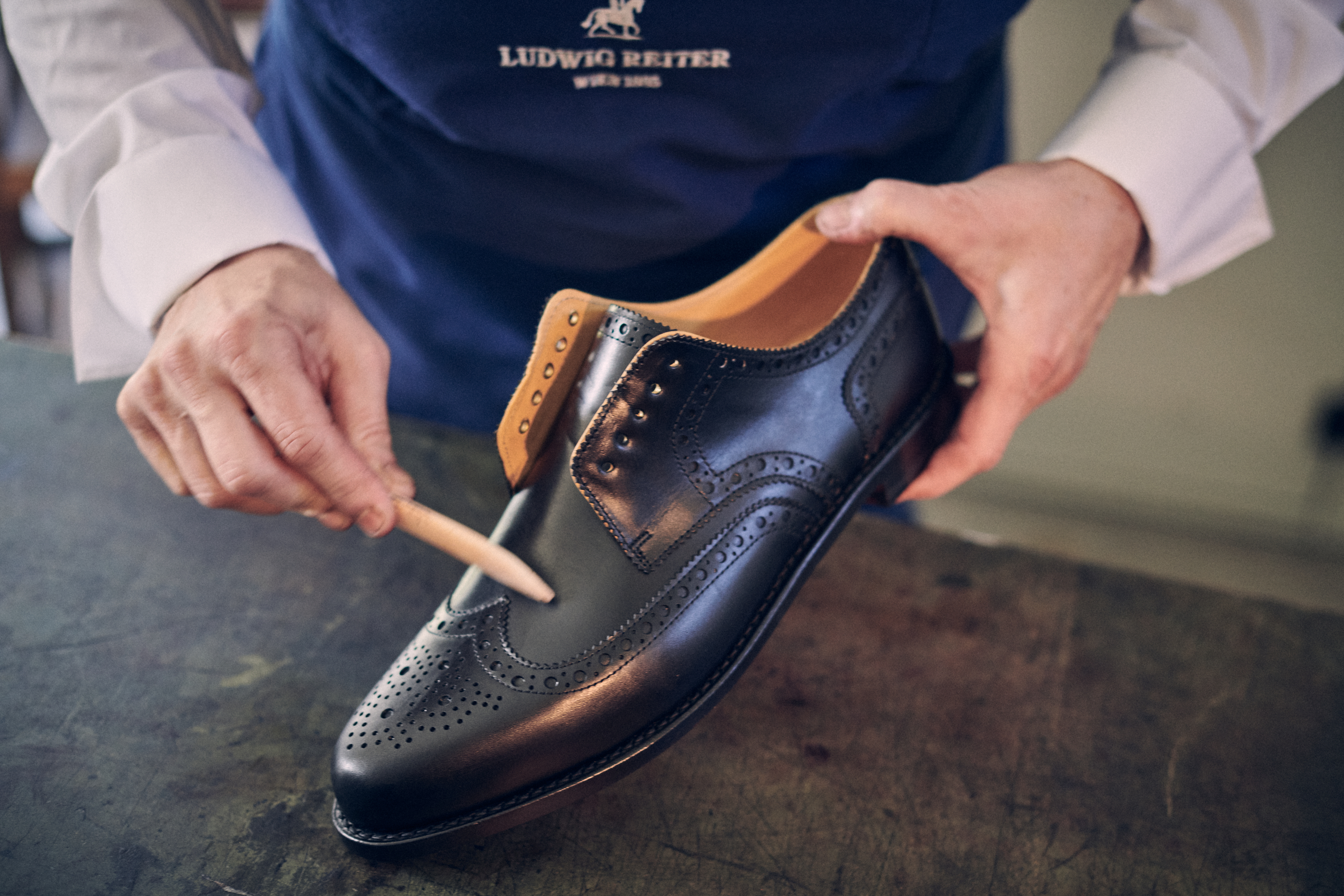
THE GOODYEAR-METHOD
In this video you can see how a welted Ludwig Reiter Budapester is created in our Viennese manufactory.
Music - Johannes Brahms, Hungarian Dance No. 8
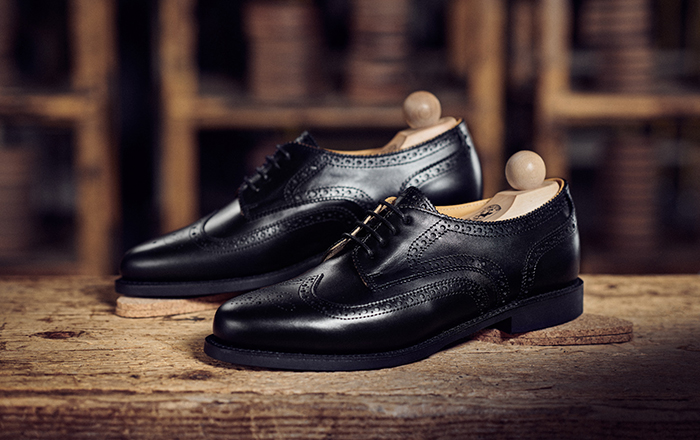
your Private order
Did you know you can personalize your Goodyear-welted Ludwig Reiter shoes?
For placing an order for custom-made shoes, we recommend to visit one of our Ludwig Reiter stores.